You have no items in your shopping cart.
Introduction to Infrared Heating Technology
Article At-a-Glance
What Are the Benefits of Infrared Heaters?
Infrared heaters offer numerous advantages over traditional heating methods, including energy efficiency, cost savings, improved product quality and consistency, increased safety, reduced maintenance, and the flexibility to customize heating solutions for specific process needs.
Key Takeaways
- Direct Heating Efficiency: Infrared heaters transfer heat directly to objects and people, bypassing air, which results in significant energy savings and reduced heat loss compared to traditional convection methods.
- Health and Wellness Benefits: These heaters can improve blood circulation, support the immune system, and reduce dust circulation, benefiting allergy sufferers and potentially offering pain relief.
- Cost-Effective Operation: With fewer moving parts, infrared heaters require less maintenance and have a longer lifespan, leading to lower operational costs and reduced need for frequent replacements.
- Enhanced Product Quality: Infrared heating provides precise temperature control and uniform heating, crucial for industries like food processing, ensuring consistent product quality and faster production rates.
- Safety and Customization: Infrared heaters offer increased safety by eliminating hot surfaces and can be customized to fit specific process heating needs, providing flexibility in installation and integration with existing systems.
Infrared heat has become popular for process heating applications in various industries. Infrared heat uses infrared radiation to transfer heat directly to the target, offering numerous benefits over traditional heating methods. The advantages of infrared heaters are evident, from energy efficiency and cost savings to improved quality control and increased safety.
This blog will explore the benefits of using infrared heaters in process heating applications and provide real-world examples of their success in various industries. Whether you're a facility manager, an engineer, or simply interested in the latest heating technologies, this blog will provide valuable insights into the benefits of infrared heating panels for your process heating needs.
Energy Savings | Cost Savings
Infrared heaters are known for their energy efficiency, which translates into cost savings for facilities that use them in process heating applications. Unlike traditional heating methods that rely on convection to heat the air, these heaters directly transfer heat to the target, resulting in more efficient energy use. This direct heating approach minimizes heat loss as an alternative to conventional central heating. It reduces the energy required to maintain a consistent temperature, making infrared heating panels a cost-effective solution for many process heating needs.
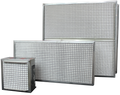
$3,835.70 USD
18" x 72" BX Series Infrared Gas Catalytic Heater 54,000 BTU/hr
In addition to its energy efficiency, infrared heat offers cost savings through reduced maintenance requirements. These heaters have no moving parts, making them less likely to break down and require repairs. They also have a longer lifespan than traditional heating methods, which reduces the need for frequent replacements and saves facilities money in the long run. Though other options like convection heaters can also solve some of these issues.
Moreover, infrared heating can also lead to lower energy bills due to their ability to quickly heat the target without overloading the heating system or wasting energy on electric convection heaters. This fast heating capability allows facilities to save energy by not having to run their heating systems for extended periods.
Overall, infrared panels' energy efficiency and cost savings make them a smart choice for facilities looking to reduce their energy costs and improve the bottom line. With their direct heating approach and low maintenance requirements, infrared heating offers a reliable and cost-effective solution for many process heating applications.
Improved Quality and Consistency of Heated Products
Electric infrared heaters can also significantly improve the quality and consistency of heated products in process heating applications. The direct infrared heating method allows for precise temperature control and uniform heating, which minimizes hot and cold spots and ensures a consistent product outcome. This is especially important in industries such as food processing, where uniform heating is crucial for food safety and quality.
In addition, infrared heating can also help improve the final product's quality by reducing the time required to heat it. This quick heating capability allows for a faster production rate, a more consistent product, and reduced energy costs.
In summary, the improved quality and consistency of products achieved through infrared heating panels make them an excellent choice for facilities looking to optimize their process heating operations. Whether in food processing, plastics manufacturing, or another industry, the precise temperature control and uniform heating provided by infrared panels can improve product quality and increase customer satisfaction.
Increased Safety and Reduced Maintenance
Infrared heaters also offer increased safety and reduced maintenance compared to traditional heating methods. Equipment failure and related safety hazards are less likely because they have no moving parts. Additionally, the direct heating approach used by infrared heating eliminates the need for hot surfaces that can cause burns or fires, making them a safer option for facilities and their employees.
In terms of maintenance, infrared heaters are low-maintenance due to their simple design and lack of moving parts. This reduces the need for frequent repairs and maintenance, saving time and resources and minimizing facility downtime.
Among the best benefits of infrared heaters, the long lifespan of infrared heating panels means that they will last longer than traditional heating methods, reducing the need for frequent replacements and associated maintenance costs.
Overall, the increased safety and reduced maintenance offered by infrared heating panels make them attractive for facilities looking to optimize their process heating operations. Infrared heating provides a reliable and cost-effective solution for many process heating needs by minimizing the risk of equipment failure and reducing maintenance requirements.
Flexibility and Customization for Unique Process Heating Requirements
Infrared heaters are highly flexible and can be customized to meet the unique requirements of various process heating applications. Unlike traditional heating methods with limited customization options, infrared heaters can be designed to fit a facility's specific needs, such as the size and shape of the heating area, the type of product being heated, and the desired temperature range.
Furthermore, these heaters can be easily integrated into existing heating systems, offering additional flexibility in placement and use. This allows facilities to maximize their heating capabilities and use these heaters with other heating methods if needed.
In addition, the compact size of these heaters also offers greater flexibility in terms of installation, as they can be placed in tight spaces or hard-to-reach areas where traditional heating methods may not fit.
The Advantages of Choosing Infrared Heaters for Process Heating Needs
The Benefits of Infrared Heaters
The benefits of using infrared heaters for process heating applications are clear. They offer numerous advantages over traditional heating methods, from energy efficiency and cost savings to improved quality and consistency of heated products to increased safety and reduced maintenance. The flexibility and customization options available with infrared heaters allow facilities to tailor their heating solution to meet their specific needs and requirements.
Choosing the right infrared heater for process heating needs can significantly improve efficiency, productivity, and cost savings, making them a smart investment for facilities looking to optimize their operations. Whether in food processing, plastics manufacturing, or another industry, an infrared heater can provide a reliable and cost-effective solution for various process heating needs.
In conclusion, the flexibility and customization options offered by infrared heaters make them a versatile solution for facilities with unique process heating requirements. Whether in a small production line or a large manufacturing facility, infrared heaters can be tailored to meet the specific needs of any process heating application.